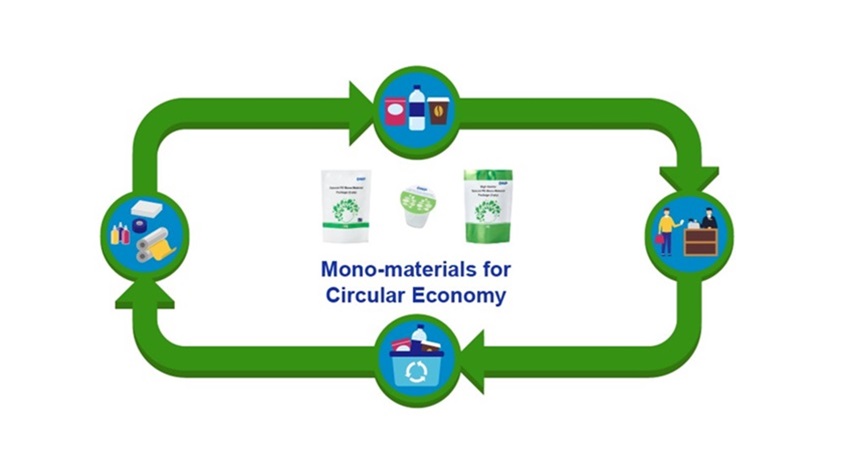
Mono-material Packaging: An Interview with DNP Indonesia, the Frontline of Development and Sales Promotions
Climate change, global warming and plastic pollution are all serious environmental problems the world is currently facing. Addressing these issues requires the development of products and services that minimize environmental impact across the entire value chain—from manufacturing to disposal and recycling—while maintaining high functionality. With demand for environmentally friendly packaging on the rise, an alternative option is “mono-materialization,” a type of packaging made from a single material to improve its recyclability. The DNP Group has established the Environmentally Conscious Products and Services Development Guidelines with the aim of reducing the environmental impact of its products and services throughout their entire life cycle. These guidelines shape the creation of environmentally friendly products and services right from the planning and design stages, with mono-material packaging being one of DNP's key innovations. At DNP Indonesia, our base for packaging-related business, we produce and sell mono-material packaging materials to meet client needs and to reduce our environmental footprint. In this feature, DNP Indonesia's Sales Junior Director and technical developers introduce the latest trends and advancements in this field.
- Advantages of adopting mono-materials
- Increased focus on mono-materials
- Strengths of the DNP Group's mono-materials-related technologies
- The future of environmentally friendly packaging paved by the DNP Group
Advantages of adopting mono-materials
Mono-material is a newly coined word consisting of “mono” (single) and "material" (indicating raw materials), meaning that a product is composed of a single material.
For example, snack packages and retort packaging for food products require many properties, such as good printability, oxygen and water vapor barriers, light shielding, heat resistance and heat-sealing*1. Until now, we have manufactured many of our products using multi-materials that combine a number of materials like aluminum foil, polypropylene (PP) and polyethylene terephthalate (PET), which all serve individual functions.
- *1: Heat-sealing property: A property that allows the resin in the innermost layer (sealing layer) of a packaging film to be sealed by applying heat and melting it. By allowing the resin to melt at a specific temperature, the speed at which the contents are filled, etc., can be adjusted.
Figure 1: Film composed of multiple materials (left) and film composed of a single material (right) |
Multi-materials are difficult to separate for recycling after use, and are disposed of in landfills or by incineration. However, as mono-materials are made of a single material, there is no need to separate the materials after use. This facilitates “material recycling,” where materials are reused in a similar manner to the original material without changing its properties.
Table: Overview and the environmental impacts for each of three types of recycling
|
Increased focus on mono-materials
![]() |
---|
A photo of the DNP Indonesia booth at Interpack 2023 (Düsseldorf, Germany) |
As of April 2024, recycling policies for plastic waste are currently underway in Europe, the world's leader in environmental policy. The European Packaging and Packaging Waste Regulation (PPWR) stipulates that packaging must be composed of recyclable materials (mono-materials) by 2030, and that sorted and collected plastics are to be recycled on a large scale by 2035. For the approximately 48% of multi-materials and other flexible consumer packaging currently on the market in Europe, recycling is being promoted by replacing polyethylene (PE) and polypropylene (PP) with mono-materials.
The U.S. has also taken steps against plastic pollution, unveiling an action plan prior to the United Nations Environment Assembly in 2022. As corporate responsibility on environmental issues faces increasing scrutiny, many global companies are now publicly committing to sustainability initiatives. A significant number of these commitments include transitioning to recyclable packaging between 2025 and 2030.
DNP Indonesia participated in Interpack 2023 (Düsseldorf, Germany) and ProPak Asia 2023 (Bangkok, Thailand), two international trade fairs and exhibitions for the packaging industry. Here, almost all global companies involved in packaging focused on improving recyclability and promoting mono-materialization.
![]() |
---|
Hendra Gunawan Ng. |
"We provide mono-material packaging to industries such as food and home & personal care. We are continuing to develop different packaging with a global consumer goods manufacturer, one of our major clients, while working to build a supply chain that extends throughout Asia, Oceania and into Africa." (Hendra Gunawan Ng)
Strengths of the DNP Group's mono-materials-related technologies
The DNP Group started developing mono-material packaging materials in 2018 and has successfully put them to practical use. In addition to being adopted for tea leaves packaging*2 for LIPTON Teas and Infusions, they have also been used in an increasing number of powdered foods, seasonings, sauces, cosmetics, laundry detergents, shampoos and other products.
|
-
*2: “Lipton Botanic Tea” and “Lipton Keep & Charge” are the products of Lipton Teas and Infusions at present.
The following are examples of adoption:
https://www.dnp.co.jp/news/detail/10158543_1587.html (Japanese article)
https://www.global.dnp/biz/solution/products/detail/10161321_4130.html
The DNP Group has continued to refine its mono-materials technology from two main perspectives. To achieve the same functions that were previously provided by multi-materials, the focus has been on maintaining heat resistance (to preserve the client’s manufacturing efficiency) and barrier properties (to ensure performance equivalent to existing packaging).
The following three core technologies are fundamental to the DNP Group’s mono-materials production.
The first is film forming technology. Our design process starts with the formulation of the base PE film or PP film that delivers the necessary functions, such as heat resistance and gas barrier properties, to produce the base material and heat-seal layer film. Next is vapor deposition technology, which involves the in-house production of vapor-deposited films. For example, aluminum evaporated in a vacuum is fixed to the surface of a film substrate to form an ultra-thin aluminum layer with high barrier properties that meet the requirements*3. In addition, barrier properties can be added through vapor deposition of silicon oxide or aluminum oxide. The third is barrier coat technology. This technology, when combined with film forming and vapor deposition technologies, further enhances the material’s ability to prevent the transmission of gases such as oxygen and water vapor. This allows for excellent aluminum-free protection against oxygen and water vapor.
- *3: The definition of mono-materials in CEFLEX, a consortium comprising more than 180 companies, associations and organizations involved in the overall flexible packaging value chain. CEFLEX aims to establish a flexible packaging market that is compliant with the EU strategy for plastics in a circular economy that includes the use of aluminum vapor deposited film to provide barrier properties.
|
Figure 2: Image of the deposition process
This technology is used to deposit an ultra-thin film by applying a substance evaporated in a vacuum onto a substrate, such as plastic film.
|
Figure 3: Image of the barrier coating process
Gravure rolls that have been engraved with an uneven surface are immersed in a coating solution. By scraping off the liquid on the roll with a doctor blade, the liquid collected in the concave area is applied to the film.
The DNP Group has developed unique fundamental technologies*4 for material processing, originally honed through our expertise in printing. By applying this knowledge to the design and production of single-material packaging, we are able to meet key requirements such as heat resistance and barrier properties for mono-material packages.
“In order to meet top-tier standards for mono-material packaging, DNP Indonesia focused on film formation and has further enhanced its technology to produce maximum results with vapor deposition and barrier coatings for enhanced functionality. We will continue to use and refine our proprietary technologies to create the mono-material packaging the world needs.” (Azusa Suzuki)
Furthermore, DNP Indonesia was one of the first companies in the packaging industry to put packaging made from recycled used plastic on the market. The company is also working to develop processes for environmentally friendly packaging that uses horizontal recycling*5.
“At DNP Indonesia, we will continue to develop optimal products while honing our world-class vapor deposition, barrier coating and film-forming technologies—proven over more than 20 years—to ensure our clients and partners continue to choose DNP products.” (Shin Yamada)
-
*4: DNP’s proprietary fundamental technology: Material processing technology that changes the shape of materials and composites them.
https://www.global.dnp/development/basic-technology/
- *5: Horizontal recycling: Refers to recycling where used products are used as raw materials to manufacture the same type of product again.
The future of environmentally friendly packaging paved by the DNP Group
The DNP Group joined CEFLEX, a consortium comprising more than 180 companies, associations and organizations involved in the value chain of the flexible packaging industry in Europe. The consortium aims to establish a flexible packaging market that supports the circular economy. We are advancing specification designs and proposals to our clients that comply with the latest guidelines.
To help stakeholders better understand the benefits of switching from multi-material to mono-material packaging, we are also working to visualize the environmental impact across the entire packaging life cycle—from raw material procurement to manufacturing, disposal and recycling.
There are also cases in which delivering products from a factory in Indonesia, rather than from a factory in Japan or other countries, can shorten the transportation distance and reduce the carbon footprint*6, which is one of DNP Indonesia's strengths.
Further reduction in carbon footprints can be expected by promoting horizontal recycling, where recycled materials are reused in packaging.
By leveraging its own advanced material processing technologies, the DNP Group is expanding its product lineup with enhanced heat resistance, barrier properties and other functionalities. We will continue to develop even more environmentally friendly products and services to reduce the use of plastics and CO2 emissions, while encouraging efficient resource use and recycling throughout the entire value chain.
- *6: Carbon footprint: The total amount of greenhouse gas emissions at each stage of a product's life cycle, such as raw material procurement, production, distribution/sales, transportation and disposal/recycling, converted to CO2 emissions. This is calculated by utilizing the life cycle assessment (LCA) method, which quantitatively calculates environmental impact.
Profile
![]() |
---|
Hendra Gunawan Ng. |
Hendra Gunawan Ng.
Since 2022, Hendra Gunawan Ng has served as Sales Junior Director of DNP Indonesia, which has a sales office and two production facilities for flexible (film) packaging and folding carton products. Working with a range of global brands, he is driving efforts to enhance sustainability by adopting mono-material packaging.
![]() |
---|
Shin Yamada (left) and Azusa Suzuki (right) |
Shin Yamada (pictured on the left)
Since 2007, Shin Yamada has been involved in the development of innovative packaging materials and manufacturing technologies, especially vapor deposition technology, at what was formerly the Packaging Research Laboratory of Dai Nippon Printing Co., Ltd. Since 2019, he has been working at DNP Indonesia as a development manager.
Azusa Suzuki (pictured on the right)
Since 2013, Azusa Suzuki has been involved in the development of vapor deposition technology, essential for improving the barrier properties of packaging materials, as well as stabilizing manufacturing conditions, including film formation, at DNP's Izumizaki Plant in Fukushima prefecture in northern Japan. He has been working as a technical expert of this technology at DNP Indonesia since 2022.
- *DNP department names, product specifications and other details are correct only at the time of writing. They are subject to change without prior notice.
October 17, 2024 by DNP Features Editorial Department
Discover more
Related products and services
DNP's Mono-material Packaging(Open in a new window)
This environmentally friendly package is made from a single material (Mono-material), maki...
DNP's Transparent Barrier Film (Open in a new window)
DNP's Transparent Barrier Film is a functional film that has superior moisture barrier and...
Related articles on the site
-
DNP Achieved Over 85% Repulpability for High Barrier Paper Mono-Material Sheet
(Open in a new window) -
DNP Achieved 190K Ton CO₂ Reduction in FY2023 with Eco-Friendly Packaging
(Open in a new window) -
DNP Selected as Constituent of FTSE4Good Global Index for 24th Consecutive Year
(Open in a new window)