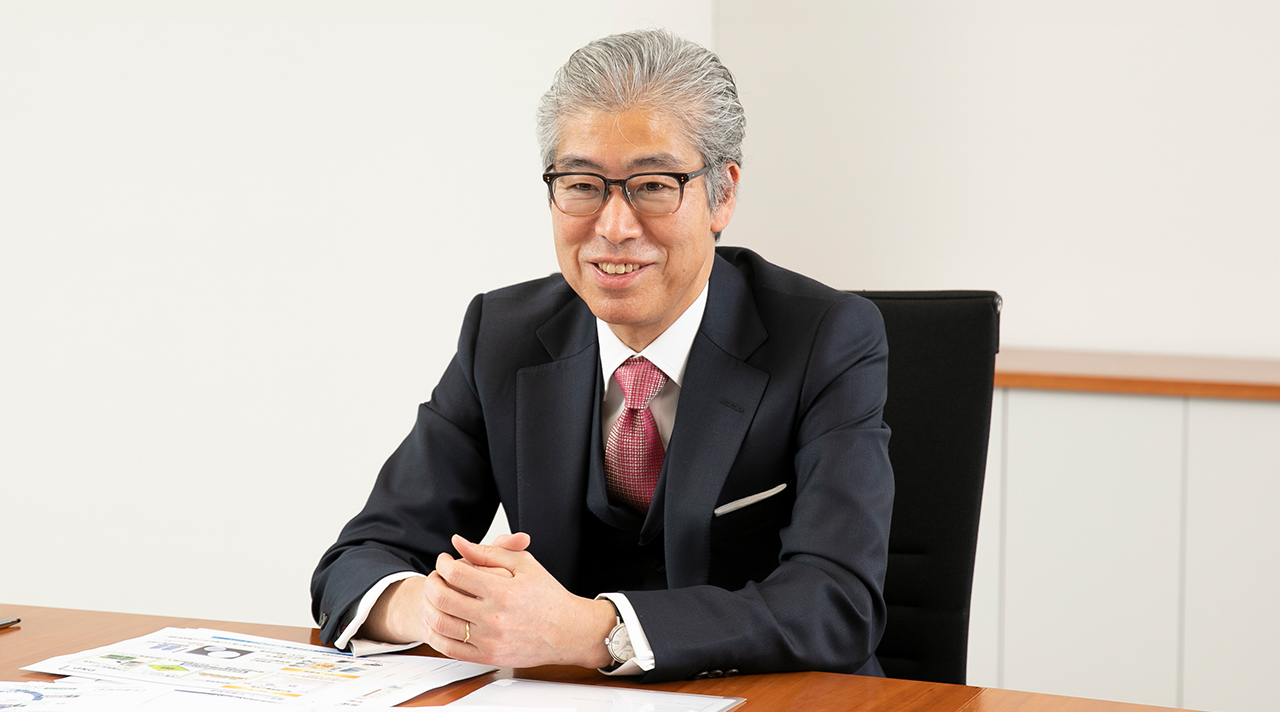
DNP’s Eco-Friendly Technologies Contribute to Realizing Carbon Neutrality
Dai Nippon Printing Co., Ltd. (DNP) formulated the DNP Group Environmental Vision 2050 in March 2020, seven months before the Japanese government publicly committed itself to attaining carbon neutrality by 2050. Ever since then, DNP has dedicated itself to realizing a society that is decarbonized, recycling-oriented and in harmony with nature to make the world sustainable and to carve out a better future. The technologies that DNP has nurtured in manufacturing serve as a pivot to advance this vision and create tangible products and services. Hiroyuki Kusukawa, who heads the Core Technology Development Division of the Research and Business Development Center, here introduces some of DNP’s eco-friendly technologies, as well as its signature products and services.
- Dawn of era of ensuring sustainability across the supply chain
- Eco-friendly applications: making biomass plastics multifunctional by combining optimal materials
- Examples in semiconductor and ICT (Information and Communication Technology) industries: high-density mounting for reducing power consumption
- Examples in mobile and battery industries: cell pouches for all-solid-state batteries to realize quick charging and high output
- DNP takes on the challenge of creating a better future with its power of technology
Dawn of era for ensuring sustainability across the supply chain
Hiroyuki Kusukawa, General Manager, Core Technology Development Division of the Research and Business Development Center |
DNP always carries out research and development of manufacturing technologies from the viewpoint of how to create and provide new value. And in recent years it has become indispensable to have a perspective of contributing to sustainability.
At a time when society is demanding sustainable products and services with low environmental impact to realize carbon neutrality, we are dedicated to developing products and services that help reduce environmental impacts across the supply chain, while producing innovative technologies that support that aim.
In manufacturing products, we adhere to the following five guidelines (Figure 1), which were formulated by considering their impact on people’s daily lives:
1) Procure sustainable raw and processed materials
2) Reduce the amounts of materials used
3) Reduce environmental impact when in use
4) Long-term usability
5) Recycling/reuse
To implement these guidelines, the entire group is introducing a wide range of measures.
Figure 1: DNP’s efforts to reduce environmental impacts with the entire supply chain in mind
|
We have produced successful results in the use of eco-friendly materials, particularly biomass materials made from plant-based raw materials (not petroleum-based), for reducing environmental impacts. We have been engaged in fruitful research and development of technologies in the following two areas. One is related to the semiconductor and ICT industries, on which the government’s Green Growth Strategy places great emphasis. The second concerns the mobile and battery industries, including batteries that are expected to be widely used in electric vehicles (EV) and other industries, as well as households.
Our latest achievements in these fields are presented below.
Eco-friendly applications: Making biomass plastics multifunctional by combining optimal materials
In the field of materials that are deeply connected with the entire supply chain, we focus on developing and manufacturing a diverse range of eco-friendly materials. To reduce greenhouse gas emissions, it is effective to use biomass plastics made from plant-based raw materials, rather than conventional petroleum-based plastics.
In 2006, we developed a biomass plastic packaging material using plant-based raw materials. In 2011, it developed the DNP’s plant-based packaging materials using a sugarcane-based raw material (Figure 2). Since then, we have been promoting practical applications of this product.
When developing it, we conducted on-site surveys at sugarcane plantations overseas based on Life Cycle Assessment (LCA), a methodology for quantitatively assessing impacts on the ecosystem and the environment. In addition, we studied the impact of consuming water resources, as the product is plant-based and requires water.
DNP’s plant-based packaging materials has physical properties equivalent to those of petroleum-based plastics. It can thus be used in place of conventional packaging in an eco-friendly manner. Currently, it is used for a wide variety of goods, successfully broadening its applications.
Figure 2: Life cycle of DNP’s Plant-based Packaging Materials
|
Using waste molasses — a byproduct of the sugarcane refining and sugar production processes — as one of the raw materials reduces the use of petroleum resources. In addition, since sugarcane absorbs CO2 when growing, the product’s entire life cycle helps to achieve carbon neutrality. |
In developing a product using a plant-based raw material, we focused on making its functions on a par with those made from petroleum-based raw materials. Since the use of plant-based raw materials usually limits the functions of plastics, we had to add functions required for packaging, such as mechanical properties (sealing strength, impact resistance, etc.) and barrier properties by means of converting technology*1 that we have developed through many years of research and development.
*1 Converting technology is a material processing technology that involves changing shapes and combining materials, for example. It refers to processing technologies, including film forming, coating, laminating, shaping, transferring, cutting, polishing, bag manufacturing, molding, and bookbinding, for materials such as paper and film.
DNP takes advantage of the extensive specialist expertise it has gained through developing and manufacturing packaging for such products as foods and daily items that can meet the standards needed to realize carbon neutrality. It then provides eco-friendly materials for a wide range of fields, from living-space products such as flooring and wall surfaces, to electronics products.
For example, we are promoting the use of biomass products that perform required functions, such as automobile sunroofs, sun visors above side windshields, and interior materials. In addition, we are developing eco-friendly features for various products such as smart cards to reduce environmental impact.
In the current era, eco-friendly materials are now a prerequisite for all industries. Being inexpensive and having good functionality are no longer just requirements demanded by customers. To swiftly meet current needs and anticipate future needs, we will remain committed to developing biomass plastics while increasing public awareness of them.
Examples in semiconductor and ICT Industries: high-density mounting with reduced power consumption
As another example of research and development of technology that realizes carbon neutrality, we manufacture semiconductor-related products by applying and advancing the microfabrication technology used for printing.
In recent years, power consumption by data centers has been rising with the spread of artificial intelligence (AI) and 5G communication services. According to one projection, power consumption by data centers will account for about 10% of that of the whole world by 2030. Against this backdrop, semiconductors must realize both higher performance and lower power consumption that are normally in a trade-off relationship.
To address this challenge, we are developing an electrical routing component (interposer) for high-density mounting of semiconductor chips (Figure 3) as a member of a consortium supported by the New Energy and Industrial Technology Development Organization (NEDO). This component allows the wiring connection of the chips to be shortened so that electrical resistance is reduced, thus enabling semiconductor products to achieve high performance and compactness.
We are in charge of developing the interposer, which is key to addressing the challenge of realizing high performance with less energy. The interposer connects semiconductor chips that are close to each other and have high density, and prevents excess power consumption by suppressing the increase in electrical resistance caused by wiring degradation. In developing the interposer, we are harnessing its diverse technologies to attain high-density mounting. One example is the development of a unique wiring protection layer technology which enhance reliability of the interposer.
Figure 3: Diagram of interposer for high-density mounting
An interposer is a technology to mount multiple semiconductor chips with differing functions, such as central processing unit (CPU) and memory, on a single package substrate at high density to enhance processing speed. The interposer developed by DNP can play a pivotal role in electrically connecting (relaying) multiple semiconductor chips to the package substrate. |
To reduce power consumption in manufacturing semiconductor products, we are also developing nanoimprint lithography*2, a manufacturing technique to press and transfer tiny patterns on a semiconductor like a stamp. In simulations conducted with partner companies, it has been shown that this technology reduces power consumption during the manufacturing process to about 10 percent of what it was before. We are on track to commercialize this product.
*2 For details on the power-saving effects of nanoimprint lithography, please click here.
DNP Features: Nanoimprint lithography accelerating carbon neutrality in semiconductor production
Examples in mobile and battery industries: Cell pouches for all-solid-state batteries to realize quick charging and high output
Just like semiconductors, batteries for electric vehicles (EVs) are essential for realizing carbon neutrality. We successfully commercialized a battery pouch for lithium-ion batteries in the late 1990s. The pouch is made of a multilayered plastic film that enables it to perform various functions. It weighs less than conventional metal cans previously used for this purpose, and battery makers have greater leeway in shaping battery cells.
We currently supply the product to Japanese and overseas battery manufacturers, and have the lion’s share of the global market. By combining technological elements involving this achievement, we are developing products for next-generation EV batteries.
DNP’s Battery pouch for lithium-ion batteries |
Achieving both quick charging and high output is both indispensable for the widespread use of EVs. This is a major challenge, as existing battery structures containing organic solvents can accumulate a large amount of energy in a short period of time, or release energy all at once, making it hot enough to catch fire. Similar problems are expected in such devices as mobile terminals, where the data volume per unit of time will increase with 5G communication services. This is therefore a problem related to social infrastructure in general, not EVs alone.
To solve this problem, the Consortium for Lithium Ion Battery Technology and Evaluation Center (LIBTEC), an industry-government-academia technical research partnership, of which DNP is a member, is developing all-solid-state batteries*3. Such batteries do not use flammable solvents and thus can achieve high fire-resistance. They can be charged quickly without cooling and other mechanisms previously required, and can deal with higher output than conventional batteries.
*3 For more information on the development of all-solid-state batteries, please click here:
DNP Features: Interview with LIBTEC President Akira Yoshino, winner of the Nobel Prize in Chemistry Part 1: Will lithium-ion batteries help solve the climate crisis?
Figure 4: Diagram of all-solid-state battery
|
Building on the expertise gained through this project, we are making our own efforts to develop packaging materials and manufacturing technologies for next-generation batteries.
DNP takes on the challenge of creating a better future with its power of technology
In order to achieve carbon neutrality by 2050, realizing a sustainable society is an urgent priority. Thinking from the perspective of people and society resonates with the founding philosophy of DNP.
We have applied and developed its strengths in the printing and information (P&I) field to provide a wide range of products and services in areas such as information and communications, lifestyle and industrial supplies, and electronics. Behind our business operations are our aspirations to solve social issues and meet people’s expectations. This is reflected in the DNP Group’s Environmental Vision 2050.
|
We believe that we must take two different approaches from a technological perspective. First is the “pioneering” approach for opening up new horizons that are unimaginable for people living in this era. Second is the “deepening” approach for creating tangible products and services in the new business fields that we have pioneered so far.
Our diverse technologies that I have explained so far, such as converting technology, material development technology, electronic module manufacturing technology, and microfabrication technology, have been developed from various printing processing technologies. Technological innovation achieved by repeatedly employing pioneering and deepening approaches has been the driving force in our efforts to generate a wide range of business areas. This pioneering approach has been led by corporate R&D department, which serves as the hub of in-house collaboration. This deepening approach has been led by various business units of DNP, each of which has its own contacts with client companies, as well as markets. These business units are therefore aware of the issues they face. They have been collaborating with each other based on their respective standpoints.
The United Nations sustainable development goals (SDGs) for 2030 include “Climate Action” and “Responsible Consumption and Production.” In 2022, keywords such as “decarbonized society” and “CPS in manufacturing” (a manufacturing system based on the interaction between cyberspace and physical space) are attracting public attention. The “common wisdom” of the manufacturing industry is thus changing drastically.
In light of this situation, we are aware that the value of technology and people’s expectations for technology are higher than ever. Based on our ALL DNP approach, we will continue taking on the challenge of creating a new and better future by leveraging our technological strengths that are widely rooted in people’s lives and society.
![]() |
---|
-
Hiroyuki Kusukawa
General Manager, Core Technology Development Division of the Research and Business Development Center
Kusukawa joined Dai Nippon Printing Co., Ltd. (DNP) in 1985. He was engaged in developing color filters for liquid crystal displays at Micro Products Research Laboratory, after which he conducted research and development mainly involving display components, such as back plates for plasma display panels and touch panel substrates. Since 2011, he has been involved in mid-term and long-term development of new products at the Research and Development Center. He has also been active in technical research associations outside the company, including serving as a director for the Japan Advanced Printed Electronics Technology Research Association (JAPERA), an auditor for the Technology Research Association for Single Wall Carbon Nanotubes (TASC) and a member of the steering committee for the Consortium for Lithium Ion Battery Technology and Evaluation Center (LIBTEC). He has held his current position since October 2021.
- *DNP department names, product specifications and other details are correct only at the time of writing. They are subject to change without prior notice.
March 22, 2022 by DNP Features Editorial Department
Discover more
Related products and services
DNP's Mono-material Packaging(Open in a new window)
This environmentally friendly package is made from a single material (Mono-material), maki...
Nano-Imprint Lithography (NIL)(Open in a new window)
Nano-Imprint Lithography is a technology that can fabricate the fine patterns required for...
Related articles on the site
-
DNP, Canon, and Kioxia Awarded Prize for Excellence at the 49th Environmental Awards for Energy-Saving Processing Technology for the advanced semiconductor manufacturing by NIL
-
DNP Develops Interposer, a Primary Component in Next-Generation Semiconductor Packaging
-
DNP Develops Photomask Process Targeting 5nm EUV Lithography